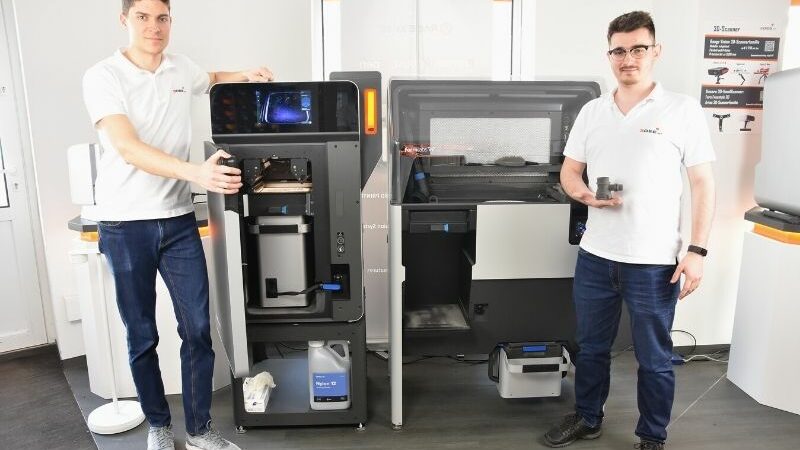
Die Fertigung von Teilen mit komplexen Geometrien ist wegen des benötigten Stützmaterials selbst für viele herkömmliche additive Verfahren eine Herausforderung. Vor allem, wenn es sich um Kleinserien handelt, bei denen eine gleichbleibende Qualität entscheidend ist.
Zur Zeit des Verfassens dieses Artikels erlebt die additive Fertigung bezüglich dieser Herausforderungen durch selektives Lasersintern (SLS) eine kleine Revolution.
Aber wie funktionieren SLS 3D-Druck Verfahren? Welche Materialien sind druckbar? Und welche Vor- und Nachteile bieten sich in der Praxis? In diesem Beitrag möchten wir genau darauf näher eingehen.
Lesedauer: 7 min
Geschichtlicher Hintergrund
In den 1980ern wurde das SLS-Verfahren von Carl Deckard und seinem Studienberater Joe Beaman an der Universität von Texas in Austin mit Finanzierung der amerikanischen Defense Advanced Research Projects Agency (DARPA) entwickelt.1
1989 reichte der amerikanische Hersteller für 3D-Drucker und Druckmaterialien “3D-Systems” ein Patent für ein ähnliches SLS–Verfahren ein.2
2001 wurde das aus der Kooperation von Deckard und DARPA entstandene Startup “DTM” von 3D-Systems aufgekauft und weiterentwickelt.3
Wie funktioniert SLS 3D-Druck?
Beim selektiven Lasersintern verschmilzt ein Hochleistungslaser ein Materialpulver zur gewünschten Form. Das Pulver wird in einem Behälter gehalten und dessen Oberfläche danach von dem Laser bestrahlt, der einen Querschnitt der Z-Achse des Objektes aus dem Pulver schmilzt. Danach wird eine neue Schicht Pulver aufgetragen, um den nächsten Z-Abschnitt darauf zu schmelzen.
Der Auftrag dieser Pulverschichten erfolgt, abhängig vom verwendeten Drucker, entweder über eine Walze oder einen Rakel. Die Schichtstärke ist im Vorhinein am Gerät einstellbar und bestimmt die Druckgeschwindigkeit und Qualität des Endproduktes. Bei hochwertigen SLS-3D-Druckern ist die Schichtstärke in einem Bereich von 1 bis 200 µm einstellbar.
Der Pulverbehälter wird Schicht für Schicht immer weiter abgesenkt. So ist das fertige Objekt dann zum Schluss vollständig von Pulver bedeckt. Das Pulver hat hierbei auch eine stützende Funktion und ermöglicht daher den Druck mit hoher Formfreiheit ohne weiteres Stützmaterial.
Der Pulverbehälter wird nach dem Druck dann samt der darin enthaltenen Teile zu einer Nachbearbeitungsstation gebracht. Dort wird das Pulver dann im ersten Schritt grob abgetragen und zur Wiederverwendung aufbereitet. Die grob entpulverten Teile werden dann mittels Druckluft von verbleibenden Pulverresten befreit und mit einem Sandstrahler Poliert. Optional können dann die fertigen Teile versiegelt und gefärbt/lackiert werden.
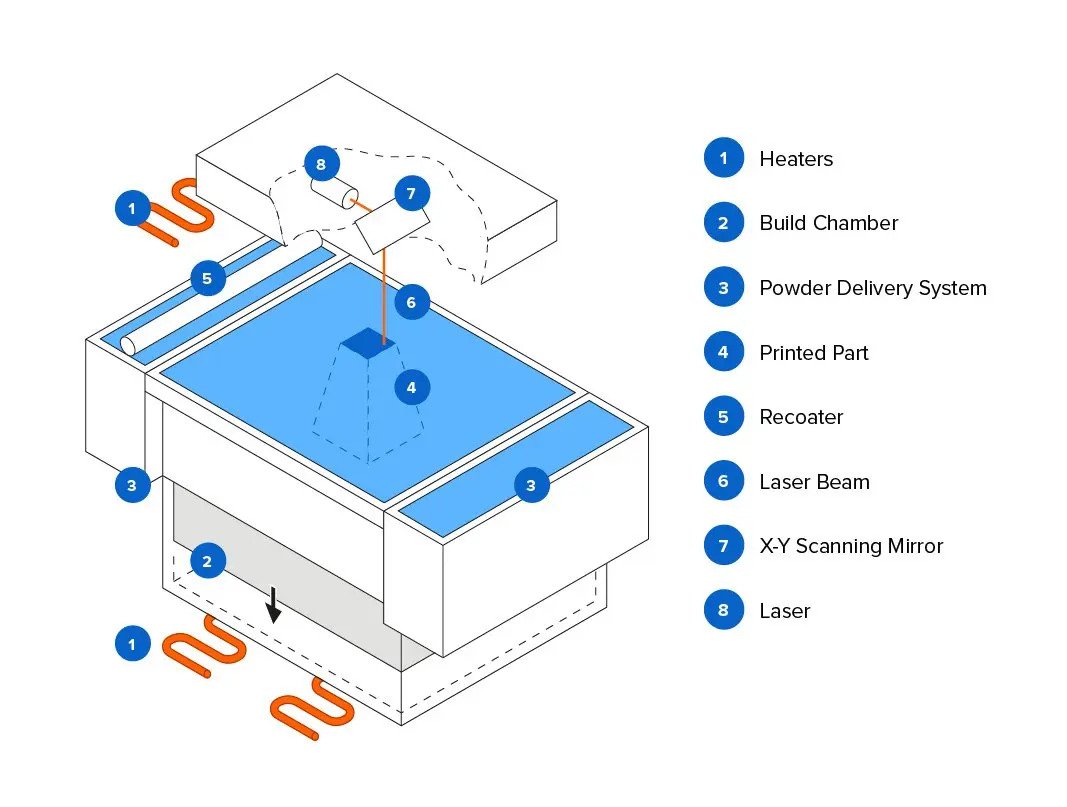
Die besten 3 SLS-3D-Drucker Hersteller
Zur Zeit des Verfassens dieses Beitrags sind vor allem drei Hersteller von hochwertigen SLS-3D-Drucker am internationalen Markt präsent. Formlabs, Sinterit und 3D Systems.
Formlabs SLS
Formlabs bietet mit dem Fuse 1 SLS 3D-Drucker sowie mit der Form Sift zur Pulverrückgewinnung und der Form Blast für Finishing ein ausgezeichnetes und gut integriertes Ökosystem für eine breite Palette an Anwendungsbereichen.
Sinterit
Sinterit bietet mit dem Lisa, Lisa X und Lisa Pro eine gute Auswahl an Formfaktoren speziell für Klein- und Mittelunternehmen. Mit dem NILS 480 hat Sinterit ebenfalls ein Gerät nach Industriestandards im Sortiment.
3D Systems
3D Systems spezialisiert sich auf rein industrielle Anwendungen. Die DMP-Serie von 3D Systems ist sogar auf Metalldruck ausgerichtet und kann nicht nur mit Stahl, Aluminium und Titan, sondern auch mit Kupfer, Kobalt-Chrom und Nickel arbeiten.
Vor und Nachteile im Vergleich zu FDM und SLA
Filament- oder uv-harz-basierter 3D-Druck braucht für komplexe Geometrien immer Stützmaterial, was nicht nur die Druckzeit und den Materialaufwand, sondern auch den Materialabfall erhöht. Beim SLS 3D-Druck braucht man durch das stützende Materialpulver keine zusätzlichen Stützstrukturen.
Vorteile
- Weitgehende Formfreiheit:
Da kein Stützmaterial gebraucht wird, können alle Winkel und Überhänge problemlos gedruckt werden. Auch innenliegende Kanäle und offene Hohlräume wie Gewinde oder Bohrungen sind für SLS kein Problem. - Effiziente Serienfertigung durch hohe Packungsdichte:
Durch das stützende Pulver können auch mehrere Objekte dicht über- und nebeneinander in den Druckraum gepackt werden. - Kostengünstige und schnelle Fertigung:
Abgesehen von den einmaligen Anschaffungskosten ist die laufende Produktion mit SLS-3D-Druckern äußerst kostengünstig und der Druckvorgang an sich vergleichsweise schnell. - Abfall-freies Arbeiten mit Pulver-Recycling
Im Gegensatz zu FDM- und SLA-3D-Druck bleibt nach dem Druck nur noch das nicht verbrauchte Pulver übrig. Dieses kann einfach gesiebt, getrocknet und wiederverwendet werden. - Homogene und isotrope Materialeigenschaften:
Beim SLS-3D-Druck werden benachbarte Pulverteilchen immer direkt und in alle Richtungen gleich miteinander verschmolzen. - Metall-3D-Druck mit speziellen Metallpulvern:
Der Laser einiger SLS-3D-Drucker ist stark genug, um ein Pulver aus Fluxus und Metallpartikeln direkt miteinander zu verschweißen. Es gibt auch Pulver aus mit Kunststoff beschichteten Metallpartikeln. Der verbundene Kunstoff muss nach dem Druck in einem Sinterofen ausgebrannt werden. - Zahlreiche Optionen in der Nachbearbeitung:
Mit SLS gedruckte Teile können problemlos gestrahlt, poliert, gefärbt oder lackiert werden.
Nachteile
- Hohe Anschaffungskosten für Gerät und Material
Beim SLS-Druck fallen vergleichsweise hohe Anschaffungskosten für Geräte und Materialien an. - Rauhe Oberfläche ohne feine Details:
Das gesinterte Pulver kann keine Details auflösen, die kleiner sind als ein Vielfaches der maximalen Partikelgröße. Diese Partikel ergeben auch eine raue Oberfläche am fertigen Druck. - Spezielle Ausrüstung für Nachbearbeitung notwendig:
Zur professionellen Nachbearbeitung von SLS-Drucken ist auf jeden Fall ein Gerät zur Pulverrückgewinnung/Entpulverung und zur Oberflächenbehandlung notwendig. - Nachbearbeitung nimmt oft viel Zeit in Anspruch:
Das Nachbearbeiten eines SLS-Drucks erfolgt oft in mehreren Schritten (Pulverrückgewinnen, Entpulvern, Sandstrahlen, Polieren und Färben/Lackieren).
Materialien für den SLS 3D-Druck
Typische Materialien für den SLS 3D-Druck sind Polyamid(Nylon)-Pulver. Oft finden sich aber auch andere Thermoplaste wie PP oder TPU in Pulverform in dem Sortiment vieler Hersteller.
Um die Materialeigenschaften dieser Pulver noch zu verbessern, werden auch häufig Kohlenstoff- oder Glas-Kurzfasern beigemengt. Diese Verbundmaterialien haben nicht nur eine höhere Festigkeit und Temperaturbeständigkeit, sondern sorgen auch für isotropische Materialeigenschaften durch eine bessere Bindung der gesinterten Schichten zueinander.
SLS-Druck für Prototyping?
Wenn sie in einem betrieblichen oder industriellen Umfeld in der Produktentwicklung arbeiten und große Mengen an einzelnen Prototypen oder von Prototypen von Baugruppen designen und testen, dann kann man SLS-3D-Druck auf jeden Fall als ein Fertigungsverfahren für diese empfehlen.
Wenn Sie jedoch nur kleine Mengen einzelner Prototypen fertigen wollen, dann reicht der Umfang nicht aus, um die langen Vorlauf- und Nachbereitungszeiten des SLS-Verfahrens zu rechtfertigen. In diesem Fall empfehlen wir Ihnen stattdessen SLA-3D-Druck.
SLS-Druck Best Practices
SLS 3D-Druck ist leider auch heute noch nicht trivial und mit viel Wartungs- und Nachbearbeitungsaufwand verbunden. Deswegen ist dieses Verfahren vor allem für Laien eher unzugänglich und ein bisschen überfordernd. Damit Sie sicher und selbstbewusst mit SLS fertigen können, möchten wir an dieser Stelle unsere jahrelange Erfahrung mit Ihnen teilen.
SLS 3D-Druck Checkliste
Vor dem Druck:
- Stellen Sie sicher, dass der Luftfilter Ihres SLS-3D-Druckers sauber ist.
- Entfernen Sie Pulverreste aus der Baukammer des Geräts.
- Säubern und überprüfen Sie die Pulverwalze.
- Befreien Sie das Laser-Fenster oder den Laser-Spiegel von Staub und Rückständen.
- Reinigen Sie die Endstücke aller Sensoren im Bauraum und überprüfen Sie diese auf ihre Funktionalität.
- Wenn Sie Materialpulver wechseln möchten, entleeren und reinigen Sie das Silo.
- Stellen Sie sicher, dass noch genug Materialpulver für den Druck vorhanden ist.
Während dem Druck:
- Falls eine Bauraumkamera vorhanden ist, überprüfen Sie von Zeit zu Zeit den Druckvortschritt.
- Überprüfen Sie auch regelmäßig den Status ihres 3D-Druckers.
Nach dem Druck:
- Entfernen Sie den fertigen Druck aus dem Bauraum.
- Tragen Sie das Pulver grob von den Druckteilen ab.
- Sieben und trocknen Sie das Pulver zur Wiederverwendung.
- Befreien Sie die Druckteile nun sorgfältig vom Rest des Pulvers.
- Bearbeiten Sie diese nach Belieben nach (sandstrahlen, färben, lackieren, …).
Profitieren Sie von unseren Services
Sollten Sie keinen SLS 3D-Drucker besitzen, oder sollte Ihnen der SLS-Workflow zu viel sein, dann nutzen Sie unseren 3D-Druck-Service. Wir bieten SLS-3D-Druck in Nylon-11, Nylon-11 mit Kohlenstoff-Kurzfasern, Nylon-11 mit Glas-Kurzfasern und Nylon-12.
Wenn Sie Fragen haben oder professionelle Beratung brauchen, zögern Sie nicht, uns zu kontaktieren!
Fazit
Die Herstellung von Prototypen und Kleinserien war früher eine kostspielige Angelegenheit. Dank moderner SLS-Verfahren profitieren immer mehr Unternehmen und Privatanwender von den Vorteilen von SLS.
Durch die vielen Vorteile von SLS-3D-Druck gibt es nun auch eine Möglichkeit für kleinere Unternehmen oder sogar Privatpersonen, Prototypen oder sogar hochwertige Produkte wirtschaftlich in-house zu fertigen.
Beratung
Referenzen und Quellen
1.) “US4863538A – Method and apparatus for producing parts by selective sintering – Google Patents.” In: patents.google.com. Abgerufen am 3. Februar 2023. URL: https://patents.google.com/patent/US4863538
2.) 3D-Systems “Unsere Geschichte”. URL: https://de.3dsystems.com/our-story
3.) “California company to acquire DTM“ für das Austin Business Journal (2001). URL: https://www.bizjournals.com/austin/stories/2001/04/02/daily10.html