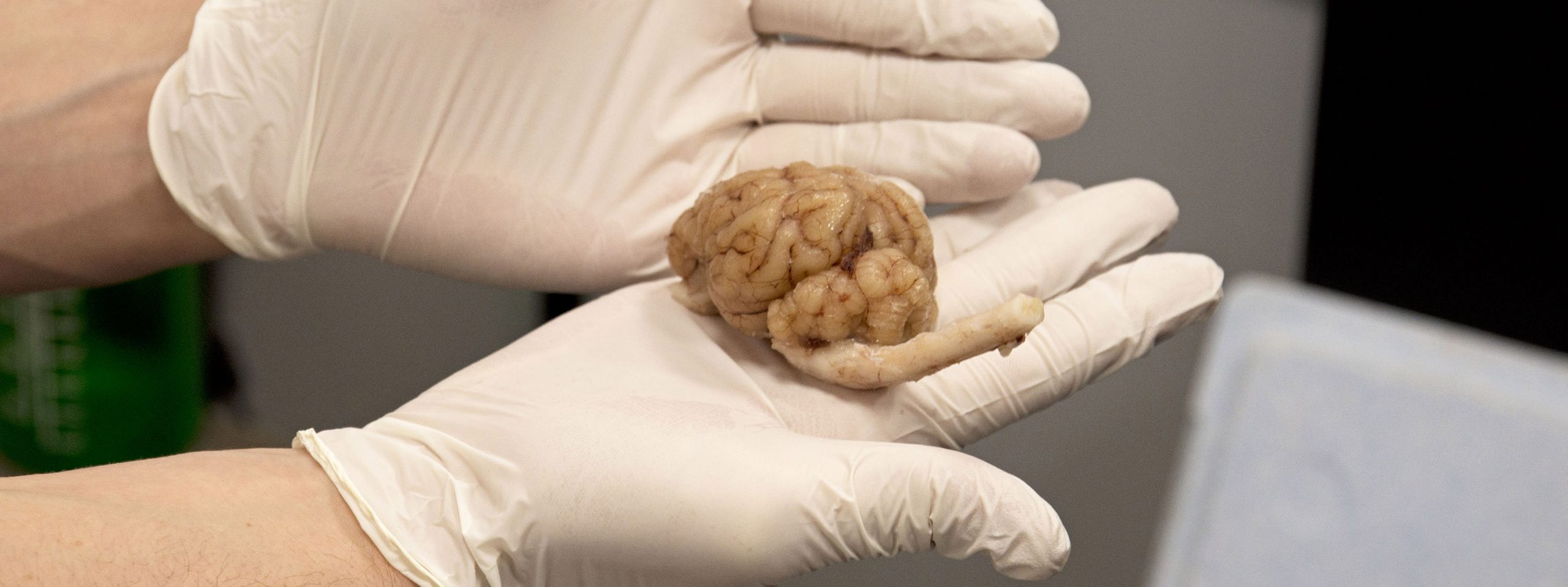
Die 3D-Drucktechnologie verbreitet sich sowohl im Bereich Medizin, als auch Tiermedizin, immer weiter. In den letzten Wochen wurden wir von der veterinärmedizinischen Universität Wien beauftragt eine tiermedizinische Schnittschablone mit 3D-Drucktechnologie anzufertigen. Einige Stunden später kommt ein tiefgekühltes Schweinehirn in unserer Werkstatt an. Das 3D-Drucken von mittels CT und MRT erstellten DICOM-Dateien ist keine Neuigkeit für uns, ein echtes Organ aus echtem Gewebe haben wir aber bisher noch nie 3D-gescannt.
Das Universitätsprojekt untersucht unterschiedliche Hirnsegmente von Hausschweinen, die Organe müssen dazu vorsichtig aufgeteilt werden. Da es sich um ein sehr weiches, empfindliches Gewebe handelt, ist bei der Segmentierung eine Schneideschablone notwendig. Konventionelle, aus Aluminium gefräste, Schablonen kosten von 1000 bis zu 2000 Euro, die Lieferzeit beträgt bis zu 6 Wochen. Im Gegensatz dazu ist die 3D-gedruckte Version im Notfall innerhalb von 14-16 Stunden einsatzbereit und kostet nur einen Bruchteil der gefrästen Versionen.
1. Schritt: 3D-Scan des Hirns
Als ersten Schritt haben wir das, auf eine Temperatur von 0° C gekühlte, Hirn auf unseren Drehteller TS12 gesetzt. Die Oberfläche des Organs ist relativ homogen, lässt aber einen relativ großen Anteil des anfallenden Lichts tiefer eindringen. Somit ist das 3D-Scannen mit der Technologie SLS (Structured Light Scanning) eine richtige Herausforderung. Um das bestmögliche Ergebnis zu erzielen haben wir den HDR-Modus aktiviert, und eine schwarze Glasplatte zur Interferenzreduzierung eingesetzt. Während dem 3D-Scannen wurden zwei 360°-Aufnahmen gefertigt, der Vorgang hat nicht mehr als 20 Minuten in Anspruch genommen, gefolgt von 10-15 Minuten Nachbearbeitung und Interferenzentfernung.
- 3D-Scanner: Range Vision 3D-Scanner
- 3D-Auflögung: 0,12 mm
- 3D-Präzision: 0,03 mm
- Zeitaufwand: 30-35 Minuten
- Software: Range Vision Scan Center
- Nachbearbeitung: Range Vision Scan Merge
- Drehteller: TS12
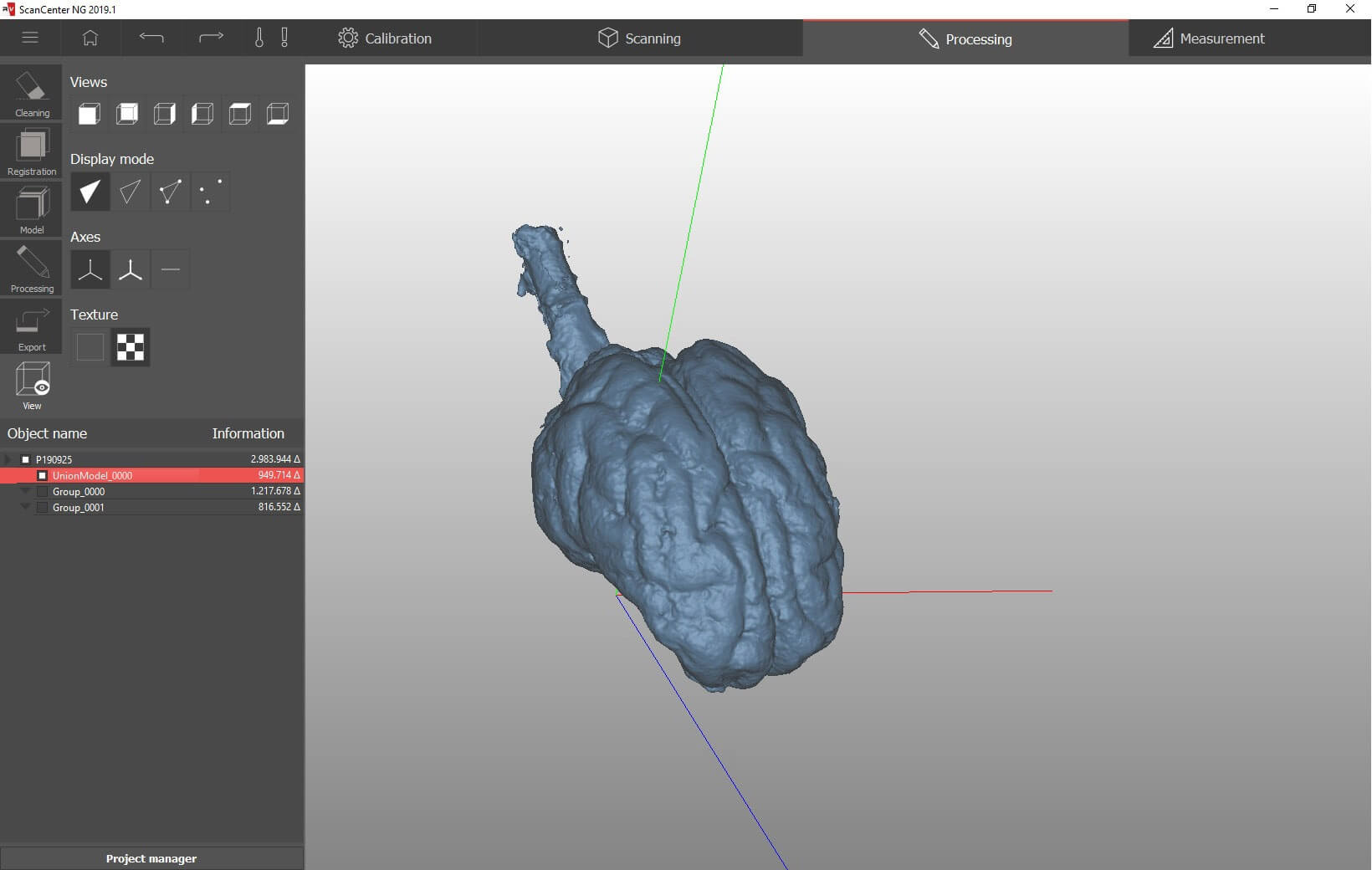
2. Schritt: Modellierung
Das mit unserem 3D-Scanner erzeugte Flächenmodell haben wir in Autodesk Fusion 360 importiert und anschließend die Schablone modelliert. Der Zeitaufwand lag bei ca. 2 Stunden. Die einzelnen Segmente sind 5 mm dick, dazwischen haben wir für das Messer (Stärke 0,5 mm) 0,6 mm breite Spalte gesetzt. Anschließend wurde die Schablone ins .stl Dateiformat exportiert und für den 3D-Druck vorbereitet.
- Software: Autodesk Fusion 360
- Dateiformat: STL
- Anzahl Dreiecke: 32162
- Dateigröße: 1571 KB
- Zeitaufwand: 2 Stunden
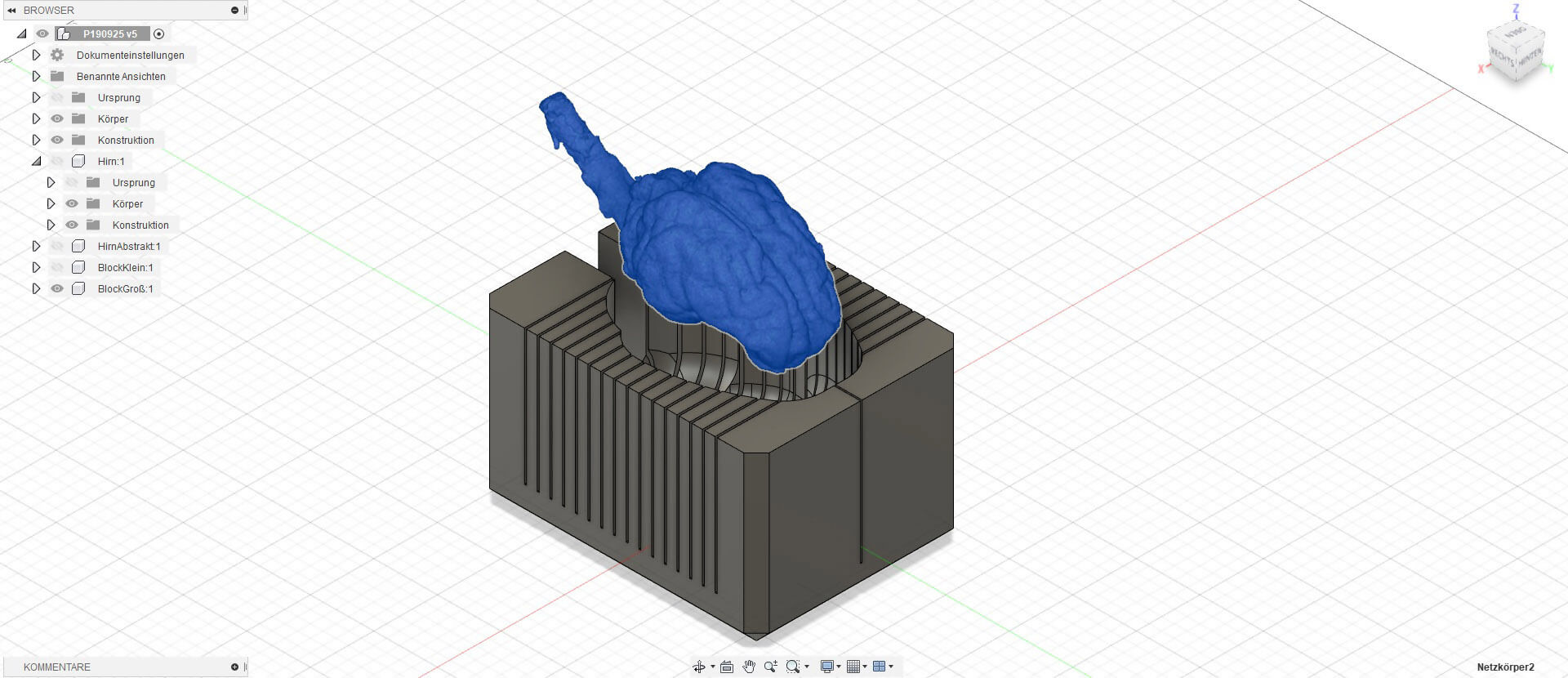
3. Schritt: 3D-Druck
Das fertige Modell der Schablone wurde anschließend mit LFS -Technologie (SLA) auf einem Formlabs Form 3 3D-Drucker aus Formlabs Grey Resin gedruckt. Der Druckvorgang dauerte mit einer Auflösung von 0,1 mm rund 10 Stunden. Dabei wurde – aufgrund der soliden Struktur – relativ viel, 394 ml, Material verbraucht was Materialkosten in der Höhe von € 51,87€ bedeutet.
- 3D-Drucker: Formlabs Form 3
- Technologie: LFS (SLA)
- Druckmaterial: Grey Resin
- Schichtauflösung: 0,1 mm
- Software: PreForm
- Druckdauer: 10 Stunden
- Materialaufwand: € 51,87 (394 ml Resin)
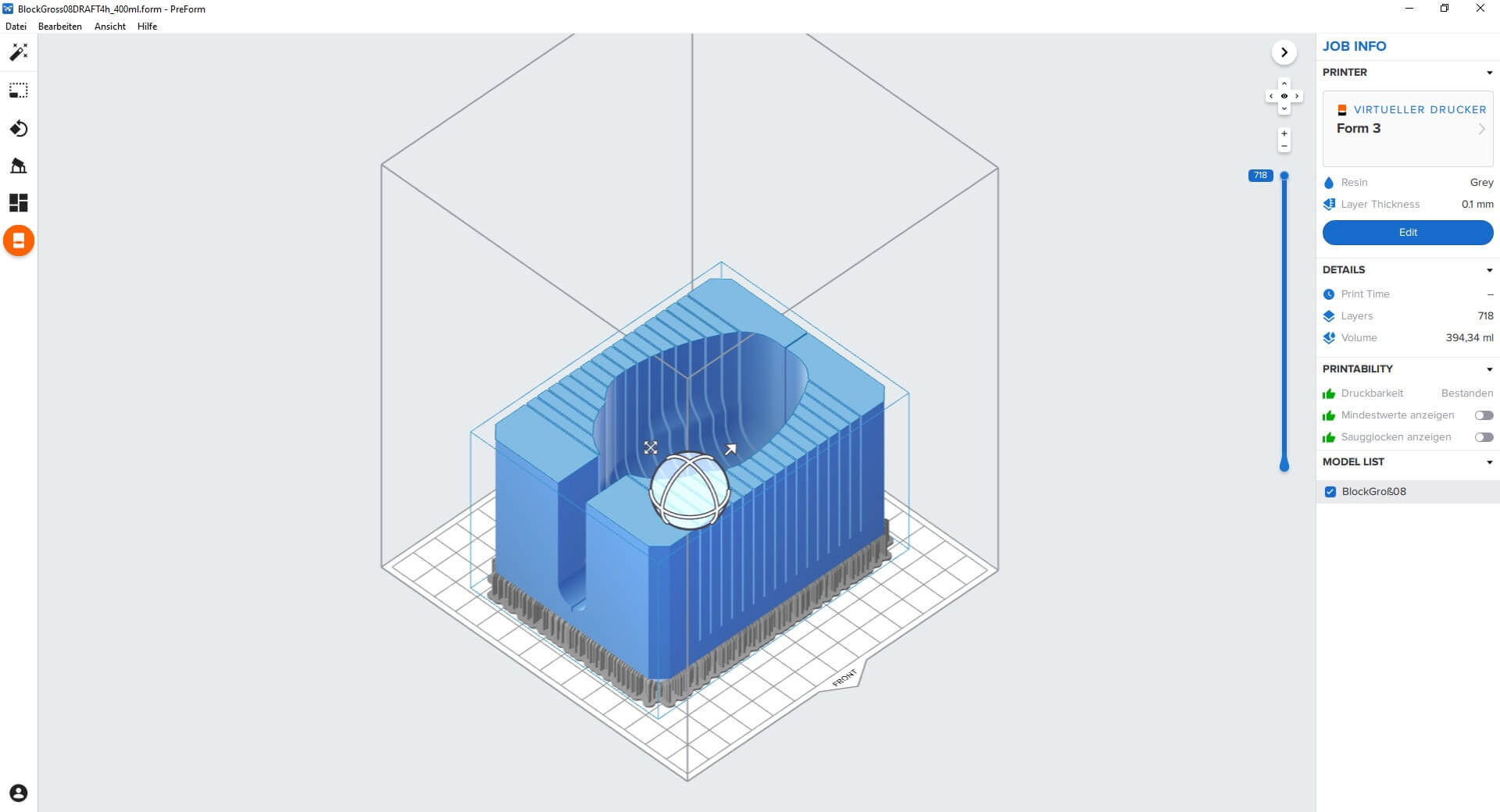
4. Schritt: Nachbearbeitung
Um die Lebensdauer und die mechanische Robustheit der Schablone zu maximieren, wurde nach dem 3D-Druckprozess eine UV-und Wärmebehandlung durchgeführt. Das ausgedruckte Modell wurde im Form Cure bei einer Temperatur von 80 °C und bei UV-Licht mit 405 nm Wellenlänge 15 Minuten lang behandelt.
- Nachbehandlung: Formlabs Form Cure
- UV-Licht: 405 nm
- Temperatur: 80 °C
- Dauer: 15 Minuten
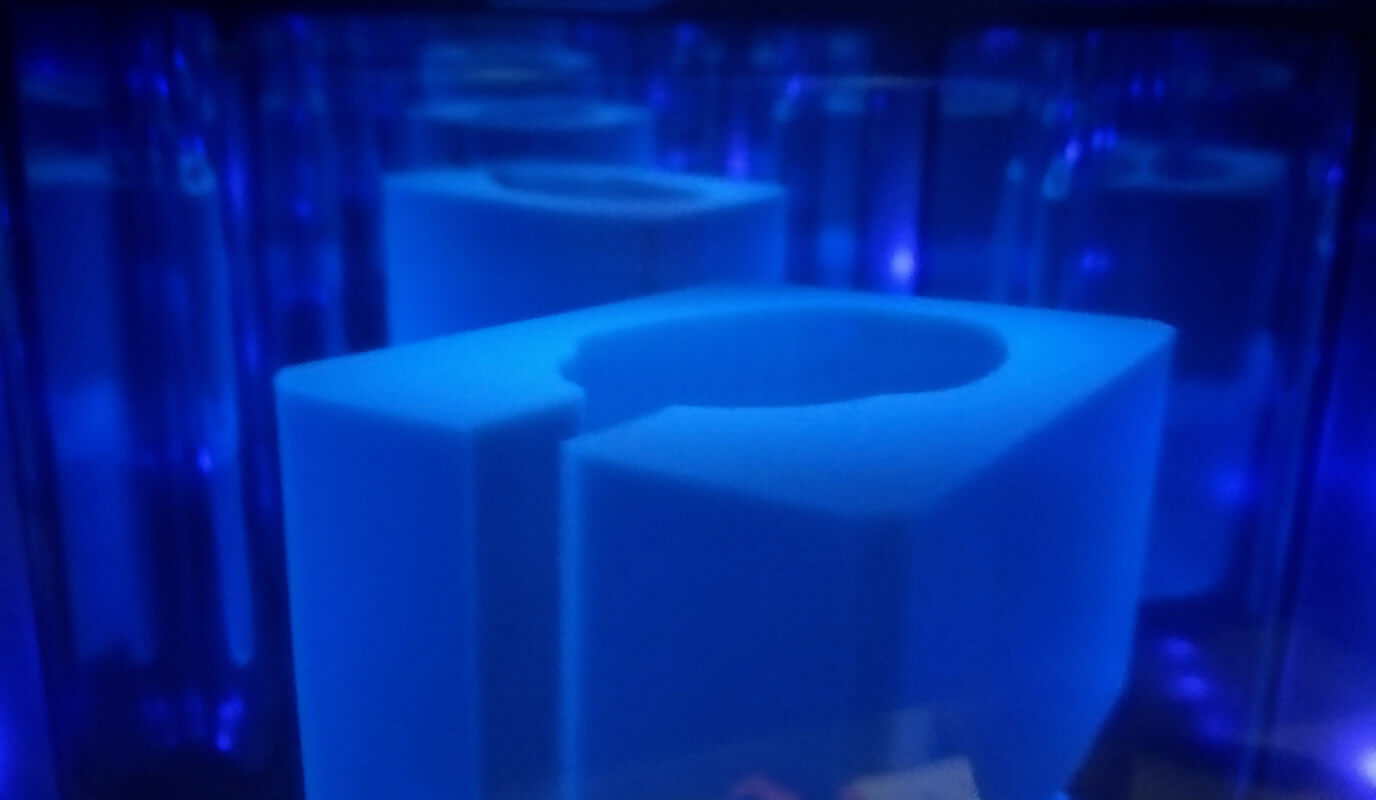
Die fertige Schneideschablone:
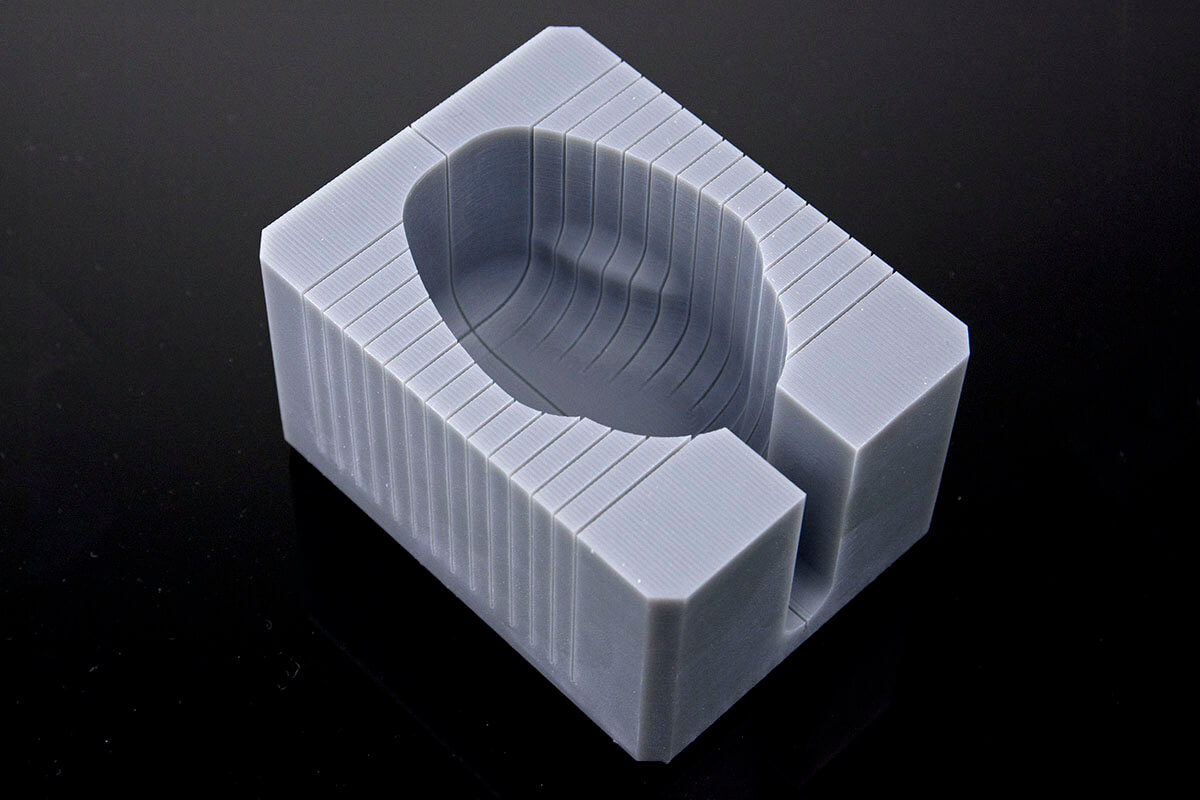
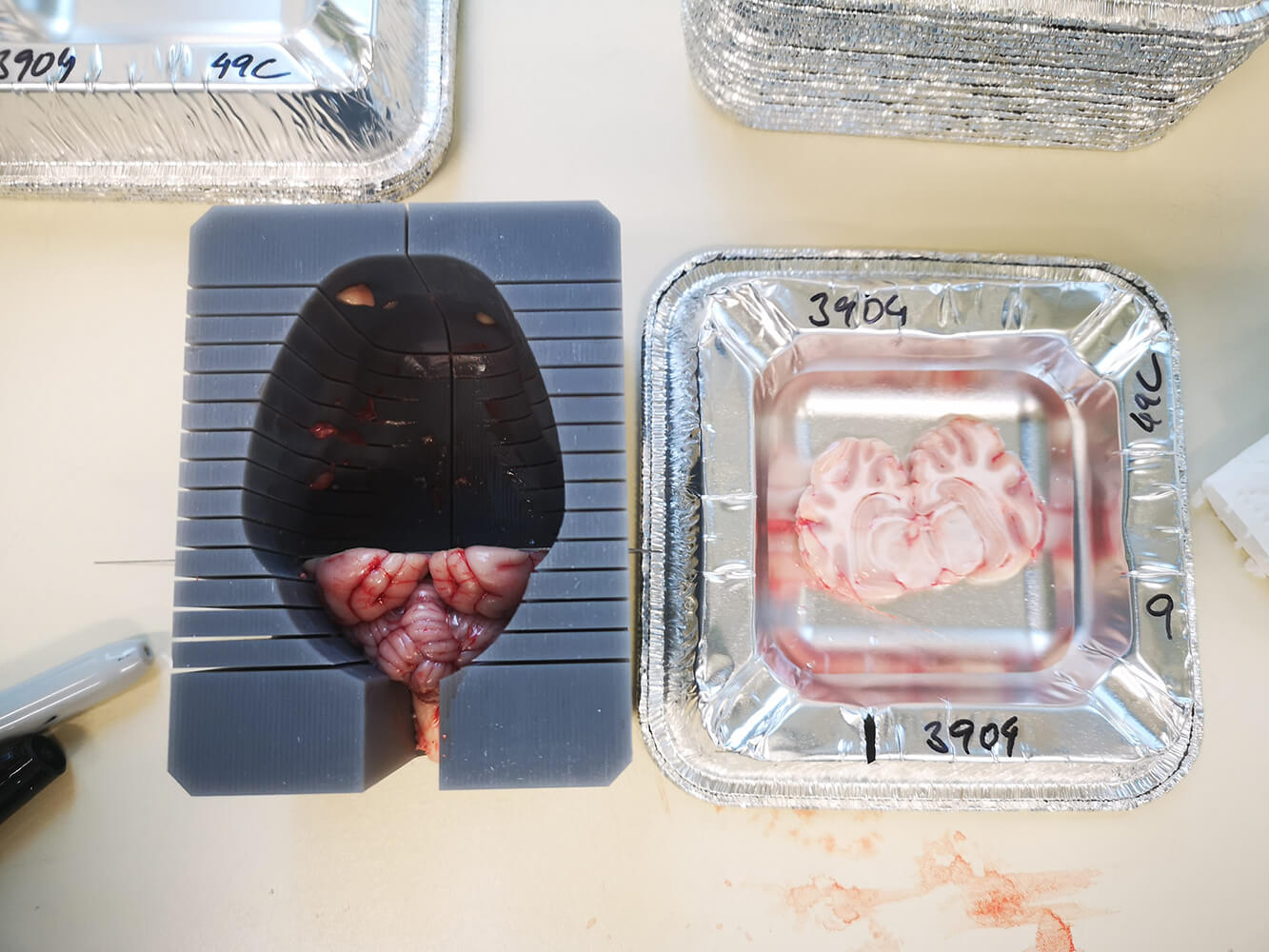